3D printing promises to transform architecture forever – and create forms that blow today's building
Not since the adoption of the steel frame has there been a development with as much potential to transform the way buildings are conceived and constructed.
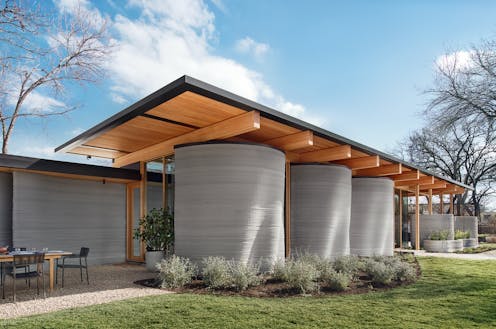
In architecture, new materials rarely emerge.
For centuries, wood, masonry and concrete formed the basis for most structures on Earth.
In the 1880s, the adoption of the steel frame changed architecture forever. Steel allowed architects to design taller buildings with larger windows, giving rise to the skyscrapers that define city skylines today.
Since the industrial revolution, construction materials have been largely confined to a range of mass-produced elements. From steel beams to plywood panels, this standardized kit of parts has informed the design and construction of buildings for over 150 years.
That may soon change with advances in what’s called “large-scale additive manufacturing.” Not since the adoption of the steel frame has there been a development with as much potential to transform the way buildings are conceived and constructed.
Large-scale additive manufacturing, like desktop 3D printing, involves building objects one layer at a time. Whether it’s clay, concrete or plastic, the print material is extruded in a fluid state and hardens into its final form.
As director of the Institute for Smart Structures at the University of Tennessee, I’ve been fortunate to work on a series of projects that deploy this new technology.
While some roadblocks to the widespread adoption of this technology still exist, I can foresee a future in which buildings are built entirely from recycled materials or materials sourced on-site, with forms inspired by the geometries of nature.
Promising prototypes
Among these is the Trillium Pavilion, an open-air structure printed from recycled ABS polymer, a common plastic used in a wide range of consumer products.
The structure’s thin, double-curved surfaces were inspired by the petals of its namesake flower. The project was designed by students, printed by Loci Robotics and constructed on the University of Tennessee Research Park at Cherokee Farm in Knoxville.
Other recent examples of large-scale additive manufacturing include Tecla, a 450-square-foot (41.8-square-meter) prototype dwelling designed by Mario Cucinella Architects and printed in Massa Lombarda, a small town in Italy.
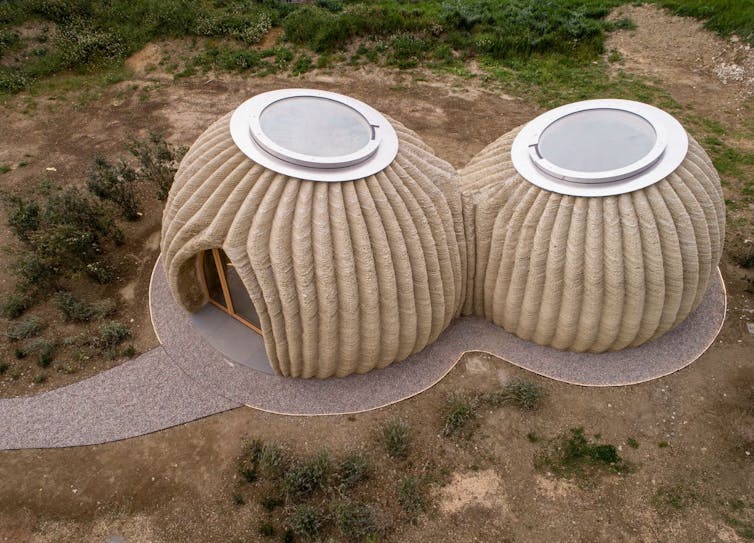
The architects printed Tecla out of clay sourced from a local river. The unique combination of this inexpensive material and radial geometry created an energy-efficient form of alternative housing.
Back in the U.S., the architecture firm Lake Flato partnered with the construction technology firm ICON to print concrete exterior walls for a home dubbed “House Zero” in Austin, Texas.
The 2,000-square-foot (185.8-square-meter) home demonstrates the speed and efficiency of 3D-printed concrete, and the structure displays a pleasing contrast between its curvilinear walls and its exposed timber frame.
The planning process
Large-scale additive manufacturing involves three knowledge areas: digital design, digital fabrication and material science.
To begin, architects create computer models of all the components that will be printed. These designers can then use software to test how the components will respond to structural forces and tweak the components accordingly. These tools can also help the designer figure out how to reduce the weight of components and automate certain design processes, such as smoothing complex geometric intersections, prior to printing.
A piece of software known as a slicer then translates the computer model into a set of instructions for the 3D printer.
You might assume 3D printers work at a relatively small scale – think cellphone cases and toothbrush holders.
But advances in 3D printing technology have allowed the hardware to scale up in a serious way. Sometimes the printing is done via what’s called a gantry-based system – a rectangular framework of sliding rails similar to a desktop 3D printer. Increasingly, robotic arms are used due to their ability to print in any orientation.
The printing site can also vary. Furnishings and smaller components can be printed in factories, while entire houses must be printed on-site.
A range of materials can be used for large-scale additive manufacturing. Concrete is a popular choice due to its familiarity and durability. Clay is an intriguing alternative because it can be harvested on-site – which is what the designers of Tecla did.
But plastics and polymers could have the broadest application. These materials are incredibly versatile, and they can be formulated in ways that meet a wide range of specific structural and aesthetic requirements. They can also be produced from recycled and organically derived materials.
Inspiration from nature
Because additive manufacturing builds layer by layer, using only the material and energy required to make a particular component, it’s a far more efficient building process than “subtractive methods,” which involve cutting away excess material – think milling a wood beam out of a tree.
Even common materials like concrete and plastics benefit from being 3D-printed, since there’s no need for additional formwork or molds.
Most construction materials today are mass-produced on assembly lines that are designed to produce the same components. While reducing cost, this process leaves little room for customization.
Since there is no need for tooling, forms or dies, large-scale additive manufacturing allows each part to be unique, with no time penalty for added complexity or customization.
Another interesting feature of large-scale additive manufacturing is the capability to produce complex components with internal voids. This may one day allow for walls to be printed with conduit or ductwork already in place.
In addition, research is taking place to explore the possibilities of multi-material 3D printing, a technique that could allow windows, insulation, structural reinforcement – even wiring – to be fully integrated into a single printed component.
One of the aspects of additive manufacturing that excites me most is the way in which building layer by layer, with a slowly hardening material, mirrors natural processes, like shell formation.
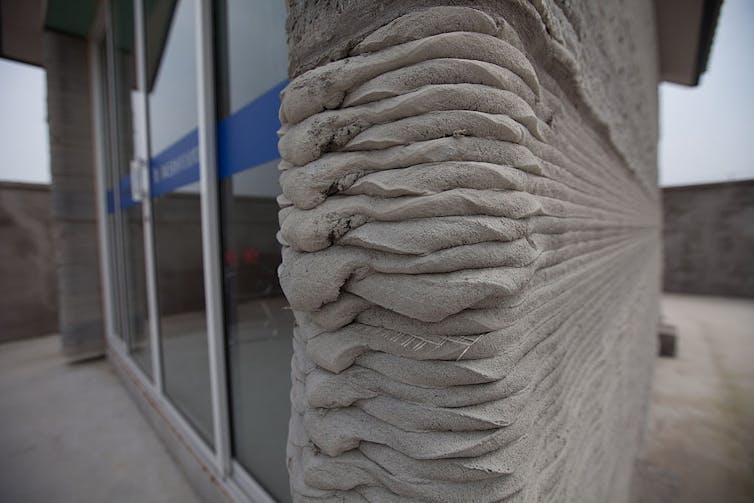
This opens up windows of opportunity, allowing designers to implement geometries that are difficult to produce using other construction methods, but are common in nature.
Structural frames inspired by the fine structure of bird bones could create lightweight lattices of tubes, with varying sizes reflecting the forces acting upon them. Façades that evoke the shapes of plant leaves might be designed to simultaneously shade the building and produce solar power.
Overcoming the learning curve
Despite the many positive aspects of large-scale additive manufacturing, there are a number of impediments to its wider adoption.
Perhaps the biggest to overcome is its novelty. There is an entire infrastructure built around traditional forms of construction like steel, concrete and wood, which include supply chains and building codes. In addition, the cost of digital fabrication hardware is relatively high, and the specific design skills needed to work with these new materials are not yet widely taught.
In order for 3D printing in architecture to become more widely adopted, it will need to find its niche. Similar to how word processing helped popularize desktop computers, I think it will be a specific application of large-scale additive manufacturing that will lead to its common use.
Perhaps it will be its ability to print highly efficient structural frames. I also already see its promise for creating unique sculptural façades that can be recycled and reprinted at the end of their useful life.
Either way, it seems likely that some combination of factors will ensure that future buildings will, in some part, be 3D-printed.
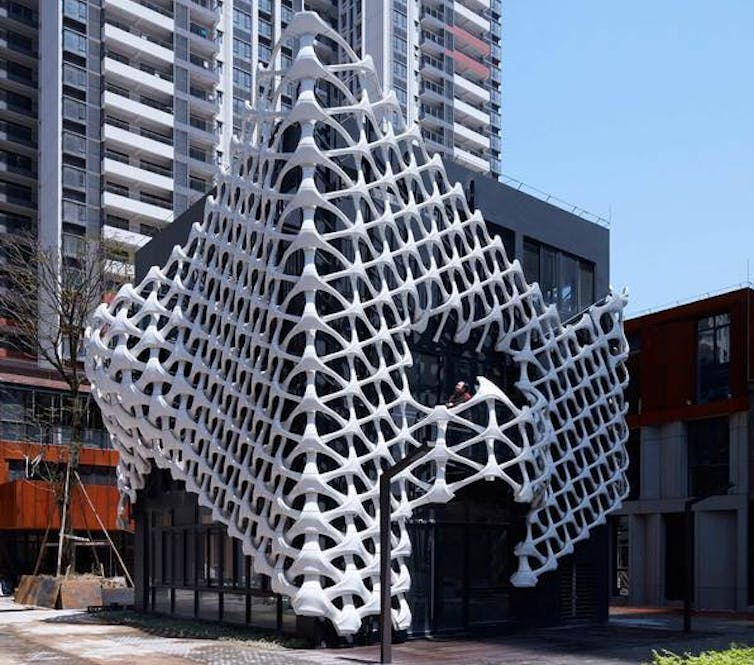
James Rose does not work for, consult, own shares in or receive funding from any company or organization that would benefit from this article, and has disclosed no relevant affiliations beyond their academic appointment.
Read These Next
Netanyahu remains unmoved by Israel’s lurch toward pariah status − but at home and abroad, Israelis
Invites are rescinded, teams and singers are booed, and citizens wonder if they should disclose their…
The ‘security guarantee’ paradox: Too weak and it won’t protect Ukraine; too robust and Russia won’t
The US and Europe hope protections for Ukraine can end the conflict. But previous attempts have fallen…
Misunderstood Malthus: The English thinker whose name is synonymous with doom and gloom has lessons
The English cleric and economist’s name is used to malign critics of progress. But historical context…